The rate of drying curve is a graphical representation that illustrates the drying behaviour of a material over time. It depicts the relationship between the moisture content of a substance and the time it takes for the material to dry under specific conditions. This curve is crucial in various industries where drying is a critical process, such as food processing, pharmaceuticals, textiles, and agriculture. Here is a detailed exploration of the rate of drying curve:
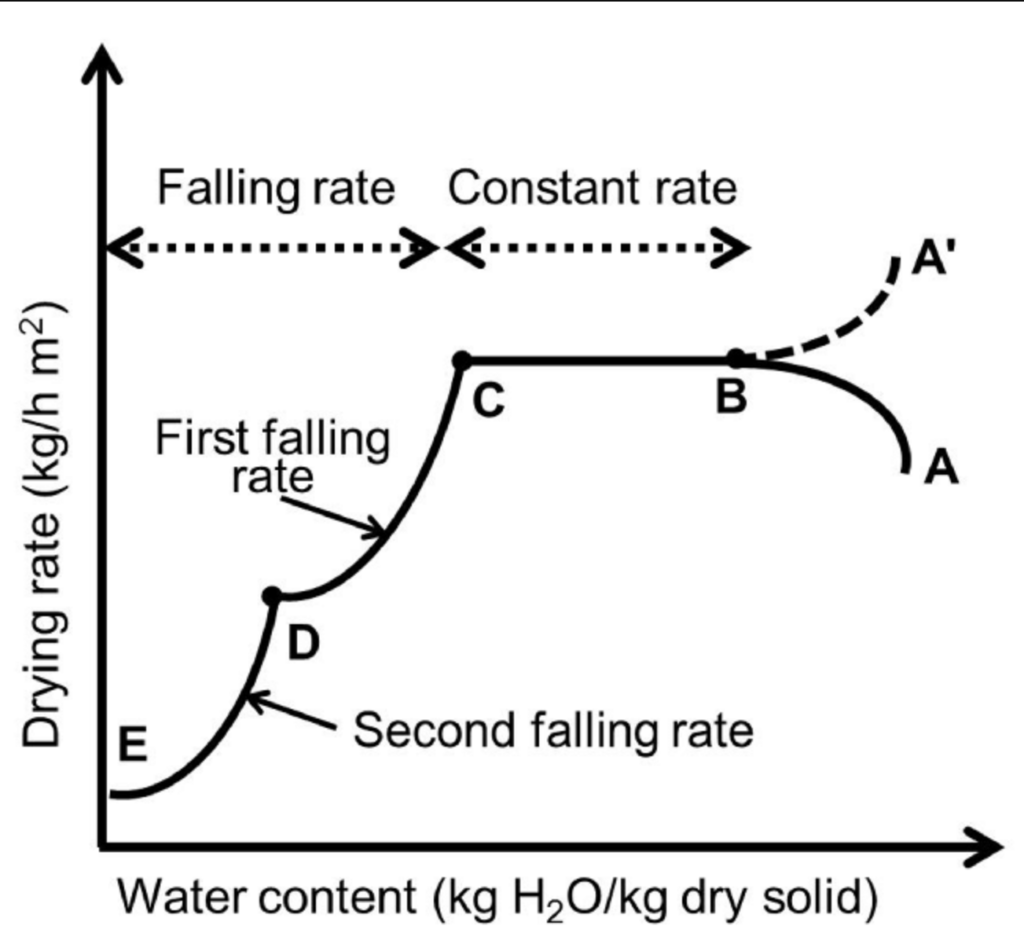
1. Y-Axis: Moisture Content (%): The y-axis of the curve represents the moisture content of the material being dried. It is expressed as a percentage of the initial weight of the material. The curve starts at 100% moisture content and gradually decreases as drying progresses.
2. X-Axis: Time (hours, minutes, etc.): The x-axis represents the time elapsed during drying. This can be measured in hours, minutes, or any other relevant time unit. The curve starts at time zero when the drying process begins.
Initial Constant Rate Period
– Description: In the initial drying phase, the moisture removal rate is relatively high and constant. This phase is often referred to as the constant rate period.
– Characteristics: During this phase, external factors such as temperature, airflow, and the material’s properties play a significant role in determining the drying rate.
– Factors Influencing: The drying rate is primarily influenced by external conditions, and the material’s surface moisture is being rapidly evaporated.
Falling Rate Period
– Description: As drying progresses, the moisture content decreases, and the drying rate slows. This phase is termed the falling rate period.
– Characteristics: The drying rate depends on the material’s internal moisture migration. Factors like diffusion and capillary action become more prominent.
– Factors Influencing: Internal resistance to moisture transfer within the material significantly influences the drying rate.
Constant Rate Period (Final Drying)
– Description: Toward the end of the drying process, the moisture removal rate may reach a relatively constant low level, indicating the final drying stage.
– Characteristics: The moisture content decreases slowly, and the drying rate becomes nearly constant.
– Factors Influencing: The moisture gradient, temperature, and airflow continue contributing to the final moisture removal.
Critical Moisture Content
– Description: The point on the curve where the falling rate period transitions to the constant rate period is crucial and known as the critical moisture content.
– Significance: It represents the point where the material undergoes a significant change in drying behaviour.
Practical Significance
– Optimization: Understanding the rate of the drying curve is crucial for optimizing drying processes. It helps set the appropriate drying conditions, such as temperature, airflow, and time, to achieve the desired moisture content efficiently.
– Quality Control: Monitoring the drying rate is essential for ensuring the quality of the final product. It helps prevent issues such as case hardening, uneven drying, and degradation of sensitive materials.
Influencing Factors
– Material Properties: Different materials have unique drying characteristics based on their composition, porosity, and structure.
– Environmental Conditions: Temperature, humidity, and airflow in the drying environment significantly impact the drying rate.
– Drying Method: The choice of drying method, whether it’s convective drying, microwave drying, or others, influences the moisture removal rate.
Instrumentation and Data Collection
– Equipment: Various instruments, such as moisture analyzers, hygrometers, and sensors, are used to collect data for constructing the rate of drying curve.
– Data Analysis: The data collected is analyzed to understand the material’s drying behaviour and to make informed decisions regarding the drying process parameters.
Understanding the rate of the drying curve is fundamental for efficient and controlled drying processes across diverse industries, enabling manufacturers to optimize production, enhance product quality, and reduce energy consumption.